大手Tier1部品サプライヤーであるA社は高い技術力と、愚直な改善活動に加え、長きに渡り多くのAutoFormプロダクトを活用し様々な技術課題に積極的に取り組まれています。超高張力鋼板への対応力強化が急速に求められる中、シミュレーション技術強化として材料データと工程再現の正確性、ロバスト性の確保を行いながらシミュレーションと実パネルとの一致率向上を達成してきました。そのような中、さらなる改善を目指し次のテーマとして“摩擦”に着目しTriboFormの評価に至りました。A社とオートフォームジャパンが共同で行った取組みとして高度摩擦モデルを考慮した評価結果を報告いたします。
【背景】
近年の自動車開発において、特に燃費向上と衝突安全性の要求は年々増加傾向にあります。北米における燃費基準を確認すると2015年:150g/kmからの10年間で90g/kmまでに規制が強化されています。これに伴い、高い衝突安全性を担保するには、安全装置が追加実装され、重量増加が避けられません。よって、今後の車両開発では、“車両軽量化”が必達の開発命題であり、プレス業界においても例外ではありません。
【内容】
日本のプレス業界における“車両軽量化”に対しての傾向として、より高い降伏点を保有する材質変更が最もポピュラーな方法として採用されています。昨今、常用されつつあるハイテンのグレードに関しても980, 1180MPa領域までの拡がりをみせています。上記に伴い、成形性、寸法精度の品質担保の為、シミュレーションの活用は必須となっています。そこで、今回は、課題が散見されるハイテンでのシミュレーション検討にて、特に“摩擦”に着目し、精度向上に取り組んだ事例を紹介します。
【摩擦課題の位置づけ】
初めに、図1.にシミュレーション精度に寄与する要因と、その寄与率を簡単に示します。当然、多くの要因が相関をもって、最終シミュレーションの品質に影響を与えていることは、間違いありません。見逃すことのできない要因として、“摩擦(トライボロジー)”が挙げられます。
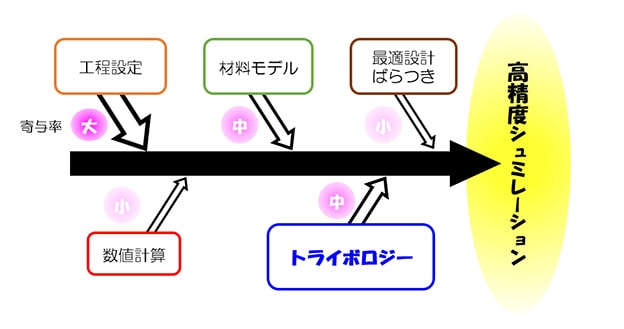
工程設定の見直しや、先進材料モデルの評価については、多くのユーザーにて日々研鑽が進んでいます。しかしながら、“摩擦”に対してのアプローチは、距離を置かれているケースが散見されています。その理由として、摩擦係数(μ)を正確にとらえる計測技術、評価閾値の妥当性を含めた仮説検証の難しさ等、多くの技術的に難しい側面があります。最大の理由としては、“どのように評価するか?”が明確でない点であると理解しています。
【背景】
昨今のハイテン化のトレンドを受け、980MPa領域までは、工程設定の見直し、材料モデル(移動硬化)の導入といった対策で、必要品質を担保されてきました。しかし、さらに高強度化が進み、1180MPa領域となった時点で、特に重要な絞り工程において、寸法精度が悪化、首振りや、捻じれといたったスプリングバック挙動の不一致が顕著化し、手直しでの工数増も避けられなくなり、更なる対策が必要と判断されました。
【目標】
1. 工程目(絞り型)精度向上 & リードタイム削減
上記2つの摩擦条件を用いたAutoFormでの計算結果と、実パネルと寸法比較を実施。
【TriboForm(ソフト)について】
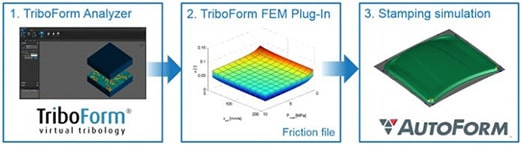
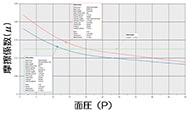
-
-
- Analyzerのみで摩擦評価可能
→各種条件変更 : 金型、シート表面粗さ(Sa)、潤滑量
→摩擦係数確認 : 面圧、速度、温度、ひずみ 4因子水準変更
→摩擦評価 : 比較検討が容易 (図2-B参照)
シミュレーション実施の前に、簡単に“摩擦”課題の把握ができます。
- Analyzerのみで摩擦評価可能
-
【評価結果】
<寸法精度>
評価部品として2部品選定し、1工程(絞り)成形後のシミュレーション結果と実パネルを、外部ソフトにより位置合わせを実施し、その際の面全体の一致率を算出しました。その際、通常(一定摩擦)とTriboFormモデルとの比較評価を実施し、その結果を図3-A.に示しています。両部品共にTriboFormモデルを採用する事で、精度向上につながりました。精度向上率としても、両部品共に同じ値を示しており、対象部品における摩擦課題の支配率もおおよそ把握できる結果となりました。次に実パネルとの最大―最小誤差を図3-B.に示しています。パネル精度誤差のばらつき低減を確認することができています。この点からもパネル全体のスプリングバックをより高精度に予測できたと推察されます。
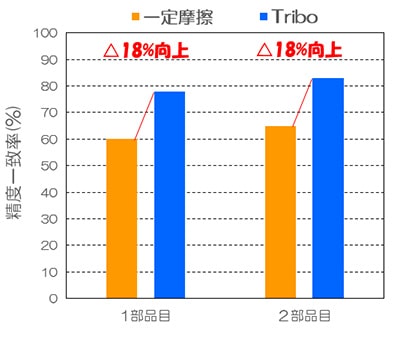
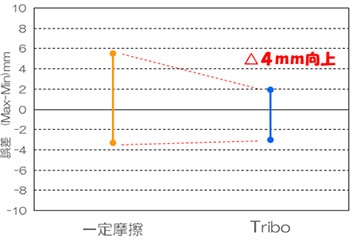
<スプリングバック挙動(首振り、捻じれ)>
補強部品系のハイテン部品によく見られる不具合として、首振りや捻じれが挙げられます。今回対象の部品においても、材料の高強度化(1180Mpa)に伴い、一定摩擦のシミュレーションと実パネルとの間で大きな差異が発生していました。図4.に首振りと捻じれの比較結果の代表断面を示しています。一定摩擦を用いたシミュレーションでは、過度に表現されてしまう現象を、TriboFormモデルを使用する事で、より実パネルに近い挙動変化を確認できました。これにより、型製作での修正回数削減によるリードタイム削減に繋がる結果となりました。
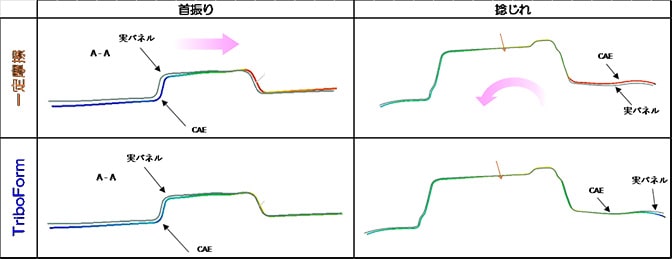
【TriboForm評価を通して】
本ケースでは、非常にスムーズな評価検討が進みました。そこで、今回の評価における重要なポイントは何処にあったのか振り返ってみます。
-
- ①摩擦(トライボロジー)が品質に与える影響を理解した上で閾値を設定
- ②評価対象のトライ日程に合わせた無理のないスケジュール設定
- ③AutoFormシミュレーションのFV設定
(FV設定:精度評価に適したパラメータ設定) - ④摩擦課題に対して深い技術デスカッション並びに困りごとを共有
大きく上記4ポイントが挙げられました。“摩擦”課題解決に限った話ではなく、因子の関連性を議論しながら理解をお互いに深めていきながら、共通のゴールを見据えたスケジュール設定など基本的な前提条件の擦り合わせを経て、スムーズで定量的な評価につながったと考えます。一方で、摩擦課題を取り扱うことは、特に③で挙げられるいわゆるシミュレーション・パラメータ設定の見直しにもつながり、総合的なシミュレーションを活用するエンジニアリング技術向上に寄与する事が確認できたと考えています。
【まとめ】
TriboFormによる効果代
-
-
-
-
-
- 1工程目(絞り型)精度向上 → △18%精度向上
- 金型改修期間削減 → △3週間短縮
-
-
-
-
上記結果から、TriboForm採用の判断に至りました。今後、同様のハイテン材にも適用させ、より詳細に摩擦因子解明に取り組まれる予定と聞いています。
各ユーザー様において対象部品、材質、シミュレーション事情は千差万別であるが、今まで目に見えず何か難しいものという印象の“摩擦”の影響代を確認する事が可能であり、対策が可能となります。“摩擦”が支配的ではないと推察される1180Mpa級ハイテン部品でも、効果代が確認されたのは、私たちにとっても大きな知見となりました。どのような対象部品でも、物理現象として“摩擦”は存在しています。TriboFormを使用した摩擦現象の理解、簡便な評価且つ、高精度なシミュレーションにご興味のある方は、是非お声がけいただきたいです。
【ユーザー様からのご感想】
・首振り量とねじれ量の見積り誤差低減により、絞り型の修正量、および以降の曲げ刃の修正量も削減でき、精度改修期間を短縮していけそうだ。
・また、超ハイテン材部品に限らず普通材の難成形部品にもTriboFormを活用し、特に割れしわ混在部位の成形対策に活用していきたい。