はじめに
プレス成形シミュレーションソフトウェアの導入から、複雑なプレス成形の工程設計や作業が変革を遂げ、その工数は大幅に削減されました。 以前はトライアウト段階で膨大なトライ&エラーを必要とした作業も、現在ではバーチャル上でのシミュレーションで効率的に実施できます。この技術革新により、エンジニアはより複雑な部品を効率的に設計できるようになりました。 しかしプレス成形のソフトウェアでデザインに微調整を加える作業や、特にスプリングバックのような複雑な不具合に関する作業などは、非常に難しく時間を要する場合があります。プレス金型を見込み補正する作業でもトライ&エラーを繰り返すため、コストや時間が膨らみます。そのためプレス成形工程で見込み補正を行う前に、そのプレス成形工程が最終アセンブリに与える影響を評価することが重要となります。この評価を通じて既存の工程に対する理解が深まるだけでなく、部品の見込み補正の代替としてアセンブリ段階を最適化する手法を確立できます。
本稿ではインドのオートフォーム社テクニカルアカウントマネージャーであるラマンディープ・シンが、インドのTire1サプライヤSKH-SMC社の非常に興味深い事例についてご紹介します。この事例はプレス成形工程ではなくアセンブリの段階で面精度を最適化することに着目し、この革新的な手法が重要かつ有効であることを示しました。
製品の仕様
この解析で使用した製品は、インドのTire1サプライヤであるSKH-SMC社がOEM向けに開発したEVバッテリーパックのセパレータプレートです。このセパレータプレートは、図1が示すとおり、2枚のプレートを組み合わせたもので、ブランクステージで生成する基盤プレートと、プレス成形工程で製造する構造プレートで構成されています。
図1. EVバッテリーパックのセパレータプレート [基盤プレート + 構造プレート]
インド発のこのプロジェクトは、オートフォーム社と長年の取引関係にあるSKH-SMC Pune社との共同研究によって進めてきました。 SKH-SMC Pune社は、OEM各社のプレス成形に関する工程設計やその調整作業に、高度な技術力を持つAutoForm製品を一貫して活用しており、その実績は高く評価されています。
この事例のOEMは電気トラックの製造を専門としています。電気トラックの駆動力はバッテリーに強く依存し、セパレータープレートで区切られたバッテリーパックを複数使用します。そのため、このプレートの設計は極めて重要です。左右のバッテリーと接触しないよう、プレートは平坦でなければなりません。さらにバッテリーのレイヤー間の距離を一定に保つため、+/- 0.5 mmの厳しい公差を満たす必要があります。
構造プレートのプレス成形シミュレーションの調査結果
SKH社の担当部署では、最終的なデザインに多数のエンボス加工が組み込まれているため、構造プレートのスプリングバックは最小限に抑制できると予測した上で、プレス成形の工程設計とシミュレーションを行いました。しかし最初のシミュレーションの結果は予測とはかけ離れたものでした。部品にはカーブがかかり、CAD0(正規寸法)のデザインとは大幅に異なる結果となったのです(図2A)。
図2A. スプリングバックを伴う構造プレートの側面図
図2B. スプリングバックを伴う構造プレートの上面図
パネルには著しいスプリングバックが生じ、偏差は最大15mmに達しました(図2B)。これはつまり構造プレートがCAD0の基準部品と同等となるように、プレス成形工程でさらに検討を重ねるべきであることを意味しています。
そのためSKH-SMC社の担当部署では、感度解析(あるいはロバスト性解析)と組み合わせた見込み補正に取り組みました。 そして製品や工程の感度によって指定の公差内で目標形状を得るのが難しくなることが分かりました。 SKH-SMC社はこの時点でインドのオートフォーム社に相談をもちかけ、ソリューションの模索を始めました。
複雑なプレス成形工程と構造プレートの最終要件を理解した上で、ラマンディープはAutoFormデジタルツインの手法を用いることにしました。これで初期アセンブリシミュレーションを実施し、既存のプレス成形シミュレーションの結果をAutoFormのアセンブリソフトウェアに組み込み、最終アセンブリへの影響を評価しました。またアセンブリ段階そのものにも改善の余地があるか評価しました。
アセンブリ最適化のソリューションを模索
アセンブリの最適化には、部品の見込み補正、シミング、ティーチングなど、いくつかの選択肢があります。
部品の見込み補正の場合、アセンブリの結果に応じて、アセンブリの1つまたは複数のコンポーネントを選択して調整します。このプロセスでは単品部品形状は通常の基準形状から外れた形状となりますが、アセンブリ後にコンポーネント全体を希望する公差内に収めることができます。
また別途、溶接治具でシミングとティーチングを併用する手法もあります。部品やサブアセンブリをオーバーベンドまたはシミングする際には、溶接スポットの適用前に、サーフェスにマイラーやクランプを使用します。一方ティーチングでは、接合用トングの位置を更新することで、新しい位置でシートに適切に接触するようにします。したがって、この手法ではクランプと接合用トングの両方を調整する必要があります。アセンブリ製品の最適化では、シミングとティーチングを併用することがよくあります。このプロジェクトでは、オートフォーム社はプレス成形工程で部品の見込み補正を行う代わりに、シミュレーションへシミングとティーチングを適用することを選択しました。
図3. マイラーに設置されたシム
アセンブリシミュレーションの結果
オートフォーム社ではプレス成形シミュレーションのデータを用いて、最初のアセンブリシミュレーションを実施しました。その結果は有望で、サーフェスの偏差が15mmから3mmに減少しました(図4)。この偏差は依然として公差限界の+/-0.5mmを超えていますが、3mmの偏差を管理する方が、プレス成形工程で15mmのスプリングバックを修正するよりもはるかに容易です。
図4. 最初のアセンブリシミュレーション後のサーフェス偏差
図5. 最初のアセンブリシミュレーション後のサーフェス偏差の断面図
動画1. アセンブリ後のドラミング効果
バーチャル環境と製造現場の初期アセンブリ工程について、その相関関係を検証する上で、動画1は視覚的に理解を深めることができる有効な手段です。アセンブリ工程後に偏差が生じ、バッテリーセパレータープレートの中央部分が上方に持ち上がる様子がこの動画からわかります。この効果はバーチャルシミュレーションでも確認され、断面ビュー(図5)に反映されています。
アセンブリ段階でのさらなる改善:
サーフェスの偏差が大きく緩和されたことで、プレス成形段階よりもむしろアセンブリ段階で最適化をさらに進める選択肢ができたのです。オートフォーム社ではさまざまな方法を試した結果、シミングとティーチングが最も効果的な手法だという結論に達し(図6)、それを推奨事項としてお客様へ伝えました。
図6. バーチャルシミュレーションのシミングおよびティーチングを通じてアセンブリの結果を改善
図7. シミングおよびティーチングを通じた第1レベルの改善後のCMMの確認(トライアウト結果)
お客様はすぐに受け入れてくださいました。プレス成形シミュレーションを繰り返す代わりに、アセンブリ段階で調整することで、スプリングバックの不具合に対処することができました。この手法は、プレス成形のトライアウトを大幅に削減できるだけでなく、シミングやティーチングによる調整は、部品の見込み補正よりもコストを抑えられるため、より費用対効果が高いことが証明されました。
アセンブリ最適化の利点
アセンブリシミュレーションを通じた最適化には、いくつかの重要な利点があります。そのいくつかを以下に示します。
- リソースの大幅削減:
シームレスなアセンブリの担保を目的としたプレス成形工程の最適化には膨大なリソースが必要ですが、アセンブリにてサーフェスの偏差を最適化すれば、プレスの最適化を回避することができます。この段階には数ヶ月かかることも珍しくはなく、満足のいく結果を得るには相当な工数やリソースがかかります。 - 扱いの容易さ:
アセンブリ工程の最適化はプレス成形よりもシンプルで制約が少ない傾向にあり ます。そのため詳細な検討やトライアルの必要性が低くなり、工程がより管理しやすくなります。 - 有効な代替ソリューション:
プレス成形で15mmのスプリングバックが生じた後にエンジニアがアセンブリの解析を行うことがなかったら、アセンブリを最適化できる可能性について気づくことはなかったでしょう。この事例はプレス成形工程のシミュレーションで満足のいく結果を得ることができない場合、特にアセンブリの最適化が有効な代替案となることを示唆しています。
まとめ
アセンブリの解析は、工程を合理化し、部品をより迅速に組み立てることができる画期的な手法であることが証明されています。シミングやティーチングなどの手法は、プレス成形ソフトウェアで見込み補正を行うよりもはるかに管理しやすいものです。プレス成形段階ではなく、アセンブリの調整を重視することで、最終部品の仕様を効率的に満たすことができます。
この手法の唯一の課題は、ソフトウェアの精度、さまざまなアセンブリ工程のモデルを作成する能力、そしてユーザーの技術力にあります。これらの要因は、アセンブリの最適化の成否を決定する上で極めて重要な役割を果たします。
<キショア・パトネイク氏より>
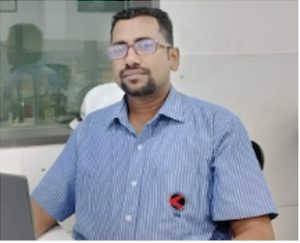
製品開発の各段階において、バーチャル領域と製造現場の相関関係を深堀りできる非常に興味深い研究でした。金型メーカーや溶接インテグレータの協力を得ながら、バッテリーパックのセパレータープレートの製造において、予期せぬサーフェスの偏差が生じない完璧な最終アセンブリを実現するという共通の目標を共有しました。
AutoFormプレス成形シミュレーションからアセンブリシミュレーションまで、そして最終的にシミングとティーチングを実施して製品を完成させるという、すべての段階で一貫した結果が得られたことに感激しました。
この非常に高揚感の高まる研究に参加できたことは、大きな喜びと満足感をもたらしてくれました!