2023年9月29日(金)ベルサール秋葉原にてAutoFormユーザー会「AutoForUm 2023」を開催いたしました。
4年ぶりの開催となった今回は、AutoForm Engineering GmbH のコーポレート・テクニカル部門担当役員のバート・カーレアから「世界で本格化するDX改革」についてのご紹介と、4社のユーザー様より、プレス成形シミュレーションの枠を超えた、最新のアプリケーション活用事例発表を頂きました。また、ユーザー様同士の交流も活発に行われ実りの多いイベントとすることができました。ご協力、ご参加いただきました皆様に感謝申し上げます。
■AutoForUm2023アジェンダ■
本記事ではユーザー会開催レポートと題しまして、残念ながら会場にお越し頂けなかったユーザーの皆さまに、発表頂いた内容の概略と会場の様子を4回にわけてご紹介します。
第1回目は、日産自動車株式会社 佛川 正哲様の講演についてご紹介します。
「AutoForm-Sigma® による量産ワレ要因の推定」
講演者:日産自動車株式会社 車両生産技術本部
プレス技術部 圧型技術課 佛川 正哲 様
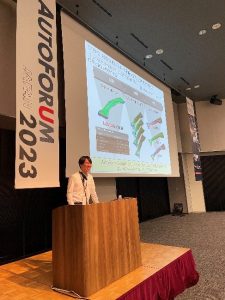
日産自動車様からは、以下2つのトピックスについて発表いただきました。
- 高精度解析を実施するためにどのような方法で要件、特に材料、摩擦、解析条件を最適化したか
- 量産ワレの要因特定のためにAutoForm-Sigmaを活用
AutoFormの予測精度を向上した上で、量産の散発ワレの要因特定と、その対策にAutoFormを活用いただいています。
※AutoFormJapanによる発表聞き取りに基づく記事ですのでご了承ください。
1. 高精度解析の要件
-材料モデルの高精度化
日産として長年取り組んでいるテーマですが、これまでは一軸引張試験による低ひずみ領域だけの考慮に留まっていました。そこで、材料モデル高精度化のために必要な各種材料試験を行うことで、高ひずみ領域まで考慮したssカーブと、引張圧縮の繰り返し試験による移動硬化則を考慮しました。さらに、等二軸引張試験結果から実験値に合うような降伏曲面の調整を行いました。
さらに、重回帰よりも高精度なサポートベクター回帰+機械学習を活用し、材料試験材とトライアウト材で特性が異なるという課題についての手法の開発を行いました。その結果、過去のトライアウト材の納入実績から、降伏応力YP、引張強さTS、全伸びELの平均値を以前よりも正しく推定することができるようになり、トライアウトの予測精度が向上しました。
-摩擦モデル高精度化
材料だけでは、なかなか次のレベルの解析高精度化が進まなかったため、摩擦の影響にも着目しました。まずは現物の状況把握からスタートするための摩擦試験を行いました。摩擦試験から採取した結果の処理には少し工夫が必要です。測定した荷重条件は、ヘルツの接触理論で荷重から面圧に変換し、摺動速度毎に面圧と摩擦係数の関係を作成しています。
得られたデータは、TriboForm Analyzerを使って AutoFormで使用できる摩擦マップを作成しています。摩擦マップは実験値に合うようなチューニングを行っています。
-解析条件最適化
品質工学の組み合わせ表を活用し、コントロール・パラメータの解析結果への寄与度を分析しました。解析設定を見直すことで高速かつ高精度な計算を実行することが出来ています。
これらの高精度化によって、ドロー工程の流入量のシミュレーションと現物の一致率の向上に成功しました。フロント・フェンダーの流入量一致率は閾値±5mmの場合67%から90%。±3mmの場合44%から69%まで向上しています。また、流入量が向上することで形状一致率も閾値±0.5mmで68%から95%に向上させることが出来ました。
2. AutoForm-Sigmaを使った量産ワレ要因分析
ARGUSによる量産ワレ保証に取り組んでいるが、生産工場で量産ワレが散発してしまう原因がわからず困っているという課題がありました。そこで、実験計画法ではなくAutoForm-Sigmaを活用し、量産ワレが発生している要因をシミュレーションで予測することにしました。ばらつきの主要因は、①材料(特性値、板厚、BL置き位置とサイズ) ②摩擦 ③ダイフェースのクリアランス の3つだと考えています。
そこで、材料と摩擦がどの程度ばらついているかを、生産工場からデータを取り寄せて分析しました。ダイフェースのクリアランスとブランク置き位置は、金型にセンサーを設置してデータを測定しました。AutoForm-Sigmaを使って、集めたこれらの量産変動パラメータを振り、ばらつき変化に弱い部位を特定しました。
ハイスペック・マシンによる並列計算で、下記のホイール・ハウス・インナー・パネルは8時間ほどで結果を取得することが出来ています。結果を見ると、量産で発生しているネッキング領域をAutoForm-Sigmaで検出出来ており、その原因が摩擦のばらつきによるものだと判断できます。不具合の要因分析がしやすいのがAutoForm-Sigmaの良いところだと思っています。
今後の課題
まだAutoForm-Sigmaでワレ検知できていない部品があります。たとえば、ボディ・サイド・アウターですが、金型の状態をより詳細に確認する必要があるかもしれないと考えています。また、工場出荷後に部品形状の変更が入っているケースもあり、どのように対処していくか検討しているところです。
今後に向けて
量産ワレの要因分析の結果を受けて、生産工場の摩擦をコントロールするために、潤滑油の量と粘度の管理するためのシステムを導入し、活用を目指しているところです。