大阪と福岡に拠点を置き、トヨタを中心とした自動車用ボディー部品のプレス金型の設計・製作を手がける株式会社ウチダ。長年にわたりAutoFormのシミュレーションソフトを活用している同社は、効率的な金型製造を目指して、オートフォームジャパンと共に既存の業務プロセスの課題を洗い出しました。100年に一度といわれる変化の激しい業界において、さらなる成長を求めるウチダは、社員1人1人のレベルアップ、特にエンジニアの技術力の強化によりトライアウト工数、コスト改善が進むことを強く認識し、“あるべき姿”の実現に向けた取り組みを始めています。
EVの台頭など「100年に一度」の大変革期、プレス金型メーカーにも大きな影響
自動車ボディー部品用のプレス金型を設計・製造するウチダは、業界のパイオニアとして常に新たな取り組みにチャレンジしています。車体の軽量化に欠かせないハイテン材(高張力鋼板)の金型成形にはどこよりも早く取り組み、超ハイテン材のセンターピラーの金型を世界で初めて実現しました。現在の主な取引先は、トヨタ・ダイハツを中心としたTier1のサプライヤーです。2020年には同社の技術力が評価され、中小企業庁による「はばたく中小企業・小規模事業者300社」に選出されました。
現在、世界中で電気自動車(EV)の開発競争が激化し、自動車業界全体が「100年に一度の大変革期を迎えています。EVシフトが進めば、自動車の部品点数は大幅に減ると言われています。エンジン車がすぐになくなるわけではないものの、中長期的にはEVの勢力が大きくなり、エンジン系、ブレーキ系、排気系の部品は厳しい状況に陥る可能性が高いと言われています。市場参入者の多様化で、日本の自動車メーカーは、EV先進国の中国、韓国、さらにはヨーロッパ、アメリカ等のライバルとの競争を勝ち抜いていかなければなりません。こうした状況に対して、代表取締役社長の内田祥嗣氏は次のように語ります。
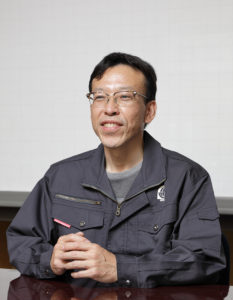
代表取締役社長 内田 祥嗣 氏
「ボディー部品の金型成形を中心とする当社は、EV化の波を今すぐに受けることはないと想定しています。とはいえ、プレス金型メーカーは、OEMメーカーや、Tier1のサプライヤーの影響を大きく受けることになり、先行きが見通せない不安は抱いています。EV化で製品ラインナップが増えれば、ボディーのデザイン変更が多く発生するかもしれませんし、短サイクルで市場に出したいという要望も増えてくるかもしれません」
目の前にある経営課題としても、カーボンニュートラルやCO2削減への対応があり、加えて資材の高騰や円安の影響も大きくなっています。こうした中、内田氏が将来に向けて最も重視しているのは、会社全体の技術レベルの底上げです。
「世の中がどのような方向に行こうとも、作る人を育て、技術レベルを高めることが一番です。私たちのミッションは取引先の期待に応えることであり、エキスパート集団としてさまざまな課題をクリアする新しいプレス金型の開発に取り組みながら、サプライヤーの成長に貢献していくことです」(内田氏)
業務プロセス(As-Is)を見直して、あるべきプロセス(To-Be)を議論
世界トップクラスの技術力を目指すウチダでは、シミュレーション技術の採用にもいち早く踏み切り、2002年にAutoFormを導入しました。現在は、AutoFormを4台、他社のシミュレーションソフト1台を利用し、AutoFormでは成形性検討を、他社ソフトでは精度見込みを行っています。
AutoFormを導入以来、オートフォームジャパンと定期的にコミュニケーションを取ってきたウチダは、両社による新たな取り組みのひとつとして、トライアウトの改善に向けたシミュレーション設定と業務プロセスのアセスメントを2021年7月から開始しました。アセスメントを通して業務プロセスの課題を洗い出し、“あるべき姿”の実現に向けて改善を図ることが目的です。デジタル技術を活用してリソースを創出し、エンジニアの技術力の向上を実現することで、金型成形の付加価値は高まり、「100年に一度」の変革期を乗り切る競争力を強化することが可能になります。次長の國原 斉氏は「シミュレーションの専門家に客観的な視点で評価していただき、改善点が洗い出せることは非常に有益だと思い、アセスメントを受けることにしました」と振り返ります。
アセスメントは、「ディスカバリー・フェーズ」として、現在の業務プロセス
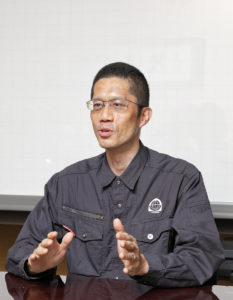
(As-Is)を洗い出すところから始まります。そして、あるべきプロセス(To-Be)を議論し、As-IsとTo-Beのギャップをどのように埋めていくことができるのかを考えていきます。ウチダでは、見積、受注から、見積、成形性検討、精度見込み、型製作、トライアウト、ホームライントライアウトまですべてのフローを洗い出し、業務フローの個々のフェーズに対してシミュレーションソフトをどのように活用しているか、そこではどのような問題が発生しているかなど、デジタル活用の実態を掘り下げていきました。
「業務フローの洗い出しや精査の作業は、2021年9月から3~4カ月かけて実施しました。具体的には、見積から型製作データ作成までの業務プロセスを、数回のインタビューをもとに作成。シミュレーション設定がトライアウトを再現するために妥当であるかをアセスメントしました。逆に、トライアウト現場を確認し、シミュレーション通りのトライアウト実施になっているかをアセスメント。さらにトライの回数、精度の修正回数、部品、顧客ごとの収益など、詳細な情報を過去1年にさかのぼって調査し、すべての資料をオートフォームジャパンと共有して現状分析を行いました」(國原氏)
SE検討における設計提案プロセスの追加でトライ回数の削減が可能
アセスメントによって自社の技術力を客観的に評価し、技術レベルの向上へ
2022年3月、オートフォームジャパンは分析した業務プロセスをもとに“あるべき姿”のプロセスを提示し、改善のポイントと、それによる見込み効果を提示しました。評価結果について、係長の桑原 拓也氏は次のように語ります。
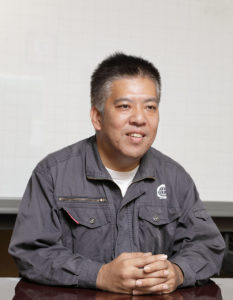
「業務プロセスについては、今までの見積工程の前に、成形性やロバスト性をシミュレーションで確認するSE検討を追加し、必要に応じて部品サプライヤーに製品形状の変更提案依頼をかけることでトライアウトの回数が減らせるという報告でした。さらに、既存の精度見込みに改善余地が多くあり、成形性検討から精度見込みまでを1本のシミュレーションソフトで統一することで効率化が進むことが分かりました。また、シミュレーションをやり切りデジタル上での金型バイオフを行うために品質基準の見直しも含めてトライアウトの回数が減らせるという分析もありました。結果として、AutoFormのソフトの追加、新たなリソースの投資が必要だとしても、数千万円のコスト削減ができることが提示されました」
SE検討における設計提案プロセスの追加は、事前の問題消し込みによる後工程の負荷軽減につながり、計り知れない効果を生む可能性を秘めています。一方で、SE検討ではOEMメーカーやTier1サプライヤーの理解と協力が不可欠であり、ウチダ単体で進めることが難しい取り組みです。
「SE検討の問題を解決するのは、簡単なことではありません。しかし、たとえばOEMメーカー、Tier1のサプライヤー、プレス金型メーカーの3者がAutoFormを共通のプラットフォームとして活用できれば、3者がAutoFormを共通言語として会話することが可能になり、全体的な効率化が実現できるのではないでしょうか」(國原氏)
一方、アセスメントの実施に対して内田氏が大きな価値を見出したのは、それが会社全体の技術力の底上げにつながることでした。
「ITツールを使うのはあくまでも人であり、ITツールによって効果的なアウトプットをすることが最終目的です。その点において、私たちはAutoFormの潜在能力を十分に使いこなせていないのではないかと不安を抱いていました。そのような中でオファーをいただいたことから、オートフォームジャパンには技術力向上への貢献を期待してアセスメントを依頼しました。今回のオファリングを通して、技術的な改善点を多く指摘していただき、解決の道筋が明確化できたことは高く評価しています」(内田氏)
内田氏の発言を裏付けるように、アセスメントの多くの過程に関わった桑原氏は「これまで私たちが独自手法で行ってきたシミュレーションとプレス品の評価方法を詳しく分析していただけたことは安心感につながりました。さらに、トライに立ち会っていただいたオートフォームジャパンの担当者が、AutoFormを使ってより詳細かつ丁寧に分析・評価している姿を見て感銘を受け、私たちも見習うべき点が多いことを改めて感じました」と語っています。
あるべきプロセス(To-Be)に向けて、さまざまな取り組みにチャレンジ
ディスカバリー・フェーズを終え、オートフォームジャパンと取り組みの実現可能性を議論したウチダでは、複数の提案の中から、第一ステップとして精度見込みフェーズにおけるAutoForm-Compensatorを使ったスプリングバック見込み業務プロセスの最適化とデジタル・スポッティングの適用によるトライアウト工数削減に取り組んでいます。
「他社ソフトとCADを使ったモデリングでシミュレーションを行う場合と、AutoFormを使った一連の流れの中でシミュレーションを行う場合のリードタイムと精度を比較するテストを実施して、ソフトをAutoFormに一本化すること、シームレスなデータフローの優位性、実際の業務プロセスに組み込む場合の実現性を探っているところです」(國原氏)
その後もあるべきプロセスに向けて、さまざまな取り組みにチャレンジしていく予定で、オートフォームジャパンには引き続きAutoFormの活用方法のアドバイス、情報提供、自動車業界に対する情報発信を期待しています。
「私たちプレス金型メーカーがSE検討に参画することで、事前の問題消し込みによる後工程の負荷軽減につながり、大きな効果が得られます。この点を業界全体にアピールしていただけばOEMメーカー、Tier1サプライヤー、プレス金型メーカーの3者がWin-Winの関係になれると思っています」(内田氏)
あるべき姿に向けて第一歩を踏み出したウチダの取り組みは、これからも続いていきます。
(企業概要)
株式会社ウチダ
設立:1964年4月
所在地:大阪府大東市新田本町12番6号
代表者:代表取締役会長 内田末男様、代表取締役社長 内田祥嗣様
資本金:3,000万円
売上高:28億円(2021年度)
従業員数:125名(2022年6月現在)
事業内容:トヨタ・ホンダ・ダイハツ・三菱・スズキなど、自動車用ボディー部品のプレス金型の設計製作全般
URL:https://www.uchidanet.co.jp/