「…怒りの中、神々は鋼の秘密を戦場に置き忘れて行った。
それを見つけた私達は、ただの人間である。
– 神でもなく、巨人でもない – ただの人間だ。
鋼の秘密には、常にミステリーがつきまとってきた。」
『コナン・ザ・グレート』ジョン・ミリアス作より
1982年にアメリカ映画となった剣と魔法の叙事詩と熱間プレス成形金型の製作会社が、どのように関係するのか知りたいですか? – ぜひお読みください。
概要
SUSTA Die Construction社は、金属加工の分野ですでに数十年の経験を有する起業家達が、自動車部品の金型製作に特化した企業として1992年に創立しました(図1)。
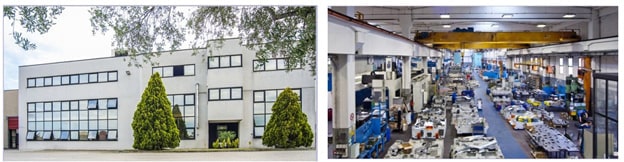
創業以来、情熱と深い知識を持ち合わせる同社は、高い品質を求める顧客からも絶大な信頼を寄せられています。またジョン・ミリアスの言葉を引用した社訓「鋼の秘密は、それを振るう者の手の中にある」は、技術へのコミットメントを強調するものです。 SUSTA社は創業当初から社員教育を重視する傍ら、最新の技術革新の動向も注視してきました。進化を求め、2009年にオートフォーム社の冷間プレス成形シミュレーションを採用し、その数年後には、デジタルの世界で熱間プレス成形工程にも乗り出しました。
今日、同社は世界最大規模のOEM各社向けに、中型から大型のさまざまな冷間・熱間プレス成形金型を生産しています。この業界では、数多くの挑戦が立ちはだかります。熱間プレス成形エンジニアのステファノ・カプリオッティ氏は、それを次のように説明してくれました。「毎日のように、私達はさまざまな分野のソリューションやサポートを迅速に提供するよう求められます。それらは、冷間および熱間プレス成形の見積もりからトライアウトまで、またプレス成形フィージビリティ解析など、多岐にわたります」。 カプリオッティ氏と彼のエンジニアのチーム、そしてトライアウト・チームが直面した最近の難題は、熱間プレス成形によるトンネル・フランジの2次成形工程でした(図2を参照)。
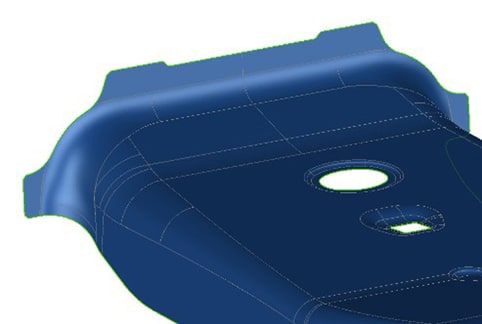
トライアウト中、1次ドロー工程にはまったく問題がありませんでしたが、後工程に問題が起きました。クエンチングで上型と下型の間の材料を冷却中に、フランジ・アップ工程で一端の最終部品形状を成形することになっていました(図3)。トライアウト・チームは、フランジ・アップした鋼材が初期位置(トップ・ストローク)に留まり、プレスから取り出した部品にフランジができていない(図4)ことを目の当たりにして、驚きとともに不安を感じました。
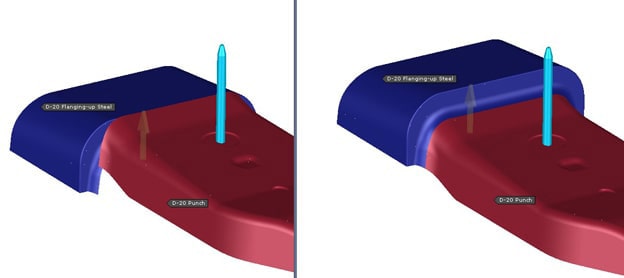
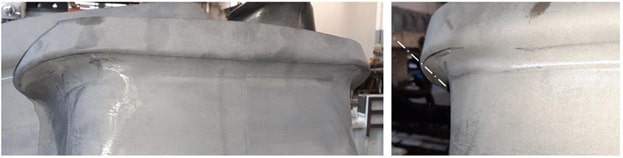
デジタル・ソリューションで、トライアウトの時間とコストを削減
プレス成形部品で品質が満たされない場合、不具合を速やかに解決するか、または少なくとも適切なソリューションを提供しなければならず、すべての関係者がプレッシャーを感じます。いまや経験は成功のために必要なもののひとつに過ぎません。ほとんどの場合、試行錯誤のループを重ねることで、再加工時間と費用が手に負えないほど膨れ上がるからです。この場合、SUSTA社の技術グループでは、AutoFormを使い、部品のフィージビリティで最も重要な最初のドロー工程を詳細にシミュレーションしました。100%マルテンサイトのトンネル形状にて、われおよびしわを回避することが、デジタル工程解析における最初の目標でした。残りの工程は、時間に応じて、シミュレーションに含めるかを選択できます。このトンネルの場合、カプリオッティ氏は、ブランクの加熱、ドロー、クエンチングおよび成形、室温までの冷却を含む、フル・サイクルのシミュレーションを設計しました。しかし、トライアウトの結果は、すべての成形ステップでシミュレーションと一致しませんでした。フル・サイクルの詳細なフィージビリティ・シミュレーションでは、ドローや2次工程で重大な成形不具合は見られませんでした(図5)。これは全く予期しないことだったと、カプリオッティ氏は認めています。「通常、成形工程では大きな違いはありません。シミュレーションのレポート内容は、その後のトライアウトで確証されます」。

「この調査に関するサポートをオートフォーム社に依頼したとき、私はシミュレーションのドロー結果(クエンチング中にフランジが成形されなかった最初の工程)と実パネルの間に、相当の関連性があることに気付きました。しかし2次工程のフランジが、なぜこれほど挙動が異なるのかを説明できませんでした。シミュレーション結果では、フランジは35KN未満で簡単に正しく成形されましたが、しかし実際のプレス機では、100KNの窒素システムで金型を持ち上げることができませんでした。私は、改めて『鋼の謎』に途方に暮れました。ソリューションにたどり着かないのは、熱間プレス成形に関する経験不足に因るのでしょうか。」
カプリオッティ氏とともに実際の工程の設定を詳細に確認してみると、いくつかの設定がシミュレーションと異なっていることが確認できました。これらの設定が「ゲームの展開」を劇的に変え、カプリオッティ氏のシミュレーションを異なる結果へと導いたのでしょうか? これを確かめる最も簡単な方法は、シミュレーション設定を修正しながらデジタル・ループを数回実行し、結果を確認することです。金型工場では、プレスの動作とフランジ金型の速度が気になったため、それらのシミュレーション設定を変更し、再度AutoFormを実行してみました。特に、加熱炉からプレス機への移動時間を延長して、ブランクの冷却を増大しました。2つめの変更点として、ブランクをパンチ・サーフェス上でもう数秒間待機させてから、ラム動作を開始するようにしました。これらの変更で、ドロー工程の開始時点での熱勾配が変化し、適正な材料相変態が得られるようになりました。AutoFormは、元のシミュレーションより100°C低い平均温度を示しました。これは、温度制御成形工程では無視できない差です。次のフランジ・アップ・ステップは、金型速度および工程のタイミングの点で、実際の工程に従ってシミュレーションしました。これは、コンポーネントの他の部分をクエンチング前ではなく、クエンチングしている間に、2次成形が行われることを意味します。実際の金型動作と解析的事象を適正に説明することで、フランジ加工を開始するために必要なブランク反力が35KNから126KNに増大しました(図6)。トライアウト・チームが実際に確認したとおり、最大能力100KNの窒素システムでは、鋼材を押し上げられません。
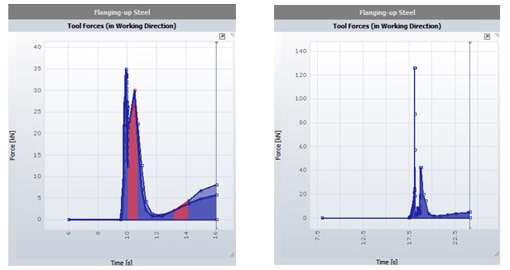
実パネルとシミュレーションの結果が一致すると、SUSTA社のプレス成形およびトライアウトのチームは、豊かな経験をもとに必要な修正を迅速かつ容易に行い、目標品質を満たす部品の生産を開始することができました。
結論
この事例から、AutoFormシミュレーションを設定する際に工程説明の精度を高めることで、トライアウトのリスクを予防できることが、改めて証明されました。ジョン・ミリアスを引用したSUSTA社の「鋼の秘密は、それを振るう者の手の中にある」という社訓は真実のようです。最も現実的で最善の結果を得るには、シミュレーションを適正に定義することが肝要であり、すべての経験とノウハウをデジタル世界でも有効活用することが必須です。試行錯誤を現実世界からシミュレーションへ移行することが、金型工場の労力と時間を軽減するための鍵となります。つまり、変動費を節減できるのです。
このようなSUSTA社の経験と日常的な成功によって、SUSTA社とAutoFormの確固な協力関係の歴史に、新たな重要なページが書き加えられました。
AutoFormイタリアとFormingWorld.comのファンの皆様に代わって、ステファノ・カプリオッティ氏とSUSTA社の皆様に、経験をシェアしていただいたことに対してお礼申し上げます。