シミュレーションを活用したインライン工程コントロールでプロセス・ウィンドウの安全圏を維持
生産ラインから取り出したプレス成形パネルにわれやしわが発生し始めたら、間違いなく流入も変化しています。チューリッヒ工科大学の仮想生産研究所(IVP)は、オートフォーム社との緊密な協働によって自動プレス・コントロールの手法を開発し、この常識を覆しました。フランケ・キッチン・システムズ社はパイロット・プロジェクトでこの画期的な手法を検証し、キッチン・シンクの深絞り中に発生する不良品の割合の削減に成功しました。
スクラップ率5%に到達
デイビット・ハーシュ博士は、「シンクのモデルによっては、熟練のプレス・オペレータでさえもパネルのスクラップを避けることができません。」と断言しています。特に半径36 mmを超えるキッチン・シンクは、成形工程間でアニーリングされないのでとてもわれやすいのです。「この不良品の割合は、小生産ロットで最大5%です」と、ハーシュ博士は強調します。
ハーシュ博士は、オートフォーム社やフランケ社と緊密に協働している仮想生産研究所(IVP)にて博士号を取得後、フランケ社のエンジニアとして開発やプロジェクトを任されています。担当業務のひとつは、キッチン・シンクの生産最適化です。フランケ社は、スイス国内のみで年間約50万台のキッチン・シンク製品を生産しています。また全世界における生産台数は年間約500万台です。同社のシンク製品には1,100種類を超えるモデルがあり、「生産バッチのサイズは非常に小さく、通常は25~200台ほどです。そのため量産時に発生しがちなスクラップを最小限に抑制することが、特に重要だと捉えています」とハーシュ博士は説明します。
図1: 左から右へ: イェルク・ハインゲルトナー博士(IVP)、アンドレアス・クレイナー(オートフォーム社)、
デイビット・ハーシュ博士(フランケ社)
シミュレーション・モデルを活用したコントロール
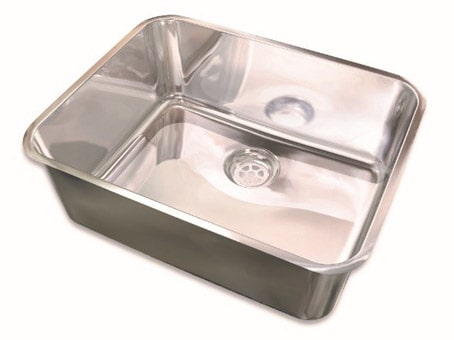
「深絞り中の工程コントロールについて、この研究所では何年も研究を続けています。」と、チューリッヒ工科大学の仮想生産研究所(IVP)で新たな生産工程の開発に取り組んでいるエンジニアのイェルク・ハインゲルトナー博士が話します。ブランク流入を測定し、それを基準流入と比較しながらプレス荷重を調整することで、品質目標を達成するこの手法は、よく知られています。「ブランク流入から品質を評価しています」とハインゲルトナー博士が説明します。「シミュレーション結果を活用して、すべてバーチャルにプレス・コントロールを設計します。そのためオートフォーム社の協力を得ているのです。」
メソッド・プランナーがコントロール・パラメータを提供
オートフォーム社製品担当責任者であるアンドレアス・クレイナーは、「当社独自のロバスト性解析ソフトウェアを使い、流入を基準値に収めるためのプレス荷重とその分布をどのように調整するか、コントロール・アルゴリズムで計算します。」と説明します。そのため、予めAutoForm-Sigmaのシミュレーションを実行し、プレス荷重と材料パラメータの両方を調整します。
「私たちは、次のような工程を想定しています。メソッド・プランナーが工程と金型を設計し、AutoForm-Sigma解析を実行してコントロール・パラメータを作成します。そしてパラメータをUSBメモリーでプレスラインに渡すのです。この結果からトン数などの工程パラメータとブランク流入の直接的な関係が明確になります。傾向を正しくモデル化できていれば、現実とシミュレーションが完全に一致する必要はありません。」とクレイナーは言います。この工程のもうひとつの利点は、ブランク流入を測定すべき位置が特定できることです。
図2:インライン工程コントロールの概略図
「生産現場では光学的手段または接触によって流入を測定できます。」とIVPのハインゲルトナー博士が付け加えます。ブルーライトを搭載したカメラを1台設置して、上方から絞るパネルの端を検出するシステムを採用しました。「シート全体の流入ではなく、オートフォーム社のロバスト性解析で特定された位置の流入のみを測定します。」
材料特性も考慮
ブランクごとに固有の材料特性は、深絞り工程の結果に大きく影響する場合があります。「フランケ社は多くのメーカーから材料を調達しています。材料によっては特性が大きく異なる可能性もあります。」とハーシュ博士は語ります。「アールブルクでは、この問題を解決するために、ブランキング金型に渦電流測定装置とレーザー測定機器を設置しました(図3)。渦電流測定装置はブランクの材料特性を測定し、レーザー測定機器はブランクの板厚を測定します。測定したデータはコントロール・システムに送信されます。工程条件のバラツキに対応する場合とは対照的に、材料の差違に対するプレス・コントロールにフィードバック・ループは必要ありません。これはAutoForm-Sigmaのメタモデルから作成し、プレス機のPLCに伝達します。各プレス・ストロークの後、カメラで測定したブランク流入を流入基準と比較し、その差異をプレス・コントローラに送り、フィードバック・コントロールを行います。この情報をもとに、次の部品に対するブランクホルダのトン数や4本のクッションピンへの荷重配分を、コントロール・アルゴリズムが計算します。AutoFormソフトウェアにはこの作業に特化したインターフェースが実装され、プレス・コントローラの設定にロバスト性の結果を利用できるようになりました。
図3: ブランキング金型に設置された渦電流測定装置およびレーザー測定機器による材料特性や板厚の測定
実際の生産現場では、この工程全体は次のように進みます。まずブランクの切断時に機械特性と板厚が特定され、それぞれのブランクに識別用のデータ・マトリックスのコードが付与されると、ブランクは山積みされます。次のプレス工程では、ブランクが1枚づつコンベヤーベルトに載せられ、データ・マトリックスのコードが読み取られると、材料特性の測定値が保存されているデータ・バンクから、そのブランクの材料特性が呼び出されます。そしてAutoFormメタモデルから、ブランクの流入基準に適合するトン数が特定されます。続いてシューラー社製の油圧プレス機(加圧能力8,000 kN)にて、ブランクが深絞りされます(図4)。さらにロボットが生産されたシンクを固定具まで運び、上方に設置されたブルーライト搭載カメラがエッジを検出します(図5)。「実際の部品と基準値を比較する際、できるだけ現実に近付けることが大切です。」とハーシュ博士が話します。「そのため進行中の生産現場では必ず優良品をデジタル化して、これをシミュレーション・モデルと比較します」。
図4: 油圧プレスの金型(シューラー社製、8,000 kN)にブランクをセットし深絞りを実施
説得力のある結果
では、すべての工程が計画通りに運んでいるのでしょうか?「基本的には、はい、計画通りです。」とイェルク・ハインゲルトナー博士は答えます。もちろん、インライン工程コントロールを使っても、スクラップを完全に回避することはできません。「すべての外れ値を考慮して、スクラップを2/3削減できたと言えます。さらに、このシステムは非常に薄いシートを処理することができ、また耐障害性もあります。検証の一環として、意図的に不正なプレス・パラメータを設定しましたが、その場合も、コントローラは非常に短時間でトン数を調整し、すぐに優良品を生産することができました。目下、フランケ社の他の工場でもインライン工程コントロールの導入が検討されています。」特にスクラップに注意すべきは、最大16片までセグメント化されたブランクホルダを使用するような複雑なプレスラインです。
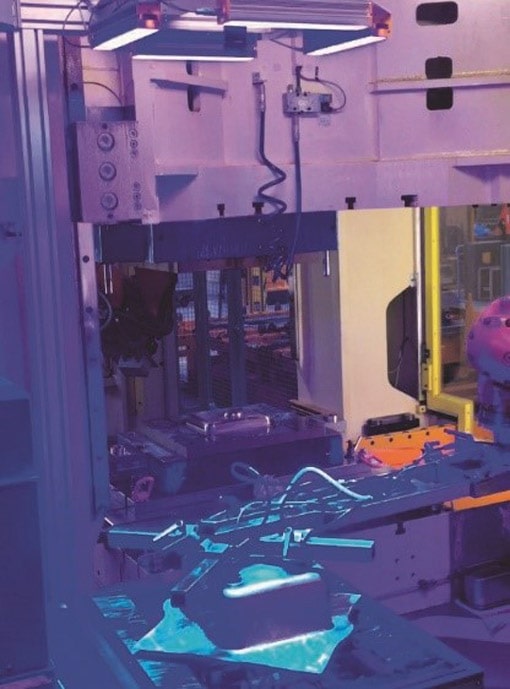
ハーシュ博士は、フランケ社が特に留意すべき重要
なポイントを指摘しています。熟達したオペレータは、それぞれのブランクや部品に適したトン数を知り尽くしています。「経験が豊富なオペレータがいなければ、複雑なモデルを許容範囲の品質で生産できなくなりかねません。」キッチン・シンクの生産は、われとしわの隙間にあるわずかなプロセス・ウィンドウ内で行われるため、量産中に金型の温度が上昇すると、すぐに不良品やプレスラインの一時停止を引き起こします。「インライン工程コントロールを併用することで、プレス成形工程が常にプロセス・ウィンドウに収まり、スクラップが皆無になります。」
フランケ社
スイスのアールガウ州アールブルクに本社を置くフランケ・グループは、家庭用キッチン、バスルーム、半公共/公共トイレ、プロのケータリング・システムやコーヒー・サーバーの大手メーカー/サプライヤーです。フランケ・グループは5大陸40ヶ国に展開し、子会社68社、およそ9,000人の従業員を擁します。