順応力と対応力による打開策: 新たな材料への挑戦
ボルボ社金型部門のCAEチームは、20年間にわたってプレス成形解析ソリューションを活用してきました。ボルボ社のXC40モデルを「フルEV」へと進化させるには、その軽量化に高強度鋼を採用せざるを得ません。しかしオロフストロムの金型工場では、この材料の取扱経験がありませんでした。この記事では、金型部門プロジェクト責任者のフレーデリック・ホーキャンソン氏による事例報告をご紹介します。
2018年、ボルボ社は名高いXC40の新型モデルとしてフルEVのXC40リチャージを発表しました。これはボルボ社では初の100%電気自動車です。ハイブリッド・モデルとは対照的に軽量化が大きな課題となり、エンジニアたちは特に安全性に関わる部分で剛性の高い材料について検討を重ね、高強度鋼を使った頑丈な構造部品が設計されました。またフルEV化によりエンジンが廃止されたため、車両前部の構造と安全性に関わる部品を一から見直す必要に迫られました。
以下のボルボ社の動画では、この新たな構造と安全性に関する取り組みについて紹介しています。
ボルボ社では、AHSSのプレス成形部品を含む複数の新規部品を、スウェーデンのオロフストロムにある自社サプライヤのボルボ社金型部門にて生産することを決定しました。しかしこれには新たな課題が山積していました。ご存じの通り、高強度鋼のスプリングバック見込み補正は厳しい公差管理が必要とされるため、高度な技術を要します。この自社金型工場では、これまでボンネット、フェンダー、ドア、テールゲートなどの部品を生産していました。新しい部品を生産するということは、すなわち、新たな課題が生じるということであり、つまり、新たなスキルが必要になるということです。
「私たちは、サイド・メンバー、Aピラー、シル構造部品、フロア部品、その他の構造部品の生産を担うことになりました。熱間プレス成形で生産していたAピラーの部品の一部が、高強度鋼へと代わります。これまで高強度鋼を使った部品の生産は、1つのプロジェクトに1つ程度しかありません。この金型工場で、これだけ多くの高強度鋼の部品を請け負ったのは初めてでした。そのため、特にスプリングバック見込み補正をデジタルとトライアウトの両方で確立するために、シミュレーションの新たなワークフローを開発しようと考えました。
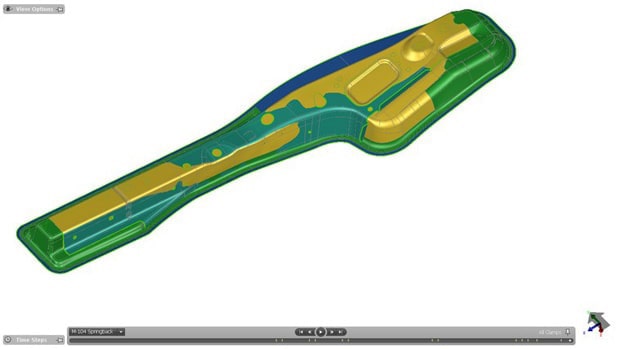
部品によっては、シミュレーションで15mm~25mmと極端なスプリングバックが発生したため、本格的な見込み補正の方案を導入する必要に迫られました。たとえば、DP800を使ったシル・インナーでは、サイドウォールに反りやねじれが生じたため、新たな材料の加工方法以外にも、新たなスキルが必要でした。そのために、AutoForm-Compensatorを導入することになりました。ボルボ社金型部門では、このソリューションを使い、深刻なスプリングバック不具合が発生している2つのAピラー、シル構造部品、2つのサイド・メンバー、計5つの構造部品を同時に検討する幅広いアプローチを取りました。
フレーデリック・ホーキャンソン氏は、以下のように説明しています。
「私達のチームには、シミュレーションについて豊富な経験があります。中には20年もAutoFormを使用しているメンバーもいます。はじめにメンバーの1人がすぐに活用方法を習得し、CAE部門のエンジニア達を指導しました。さらにはオートフォーム社の協力体制も大きな支えでした。まずは初期フィージビリティの検討を行い、次の段階では、シミュレーションで確認されたスプリングバックに対応するために見込み補正を行いました。さらには部品を公差に近付けるため、実パネルをスキャンしたデータを『一般の見込み補正』にインポートしました。そしてこれが、新たなワークフローとなりました。」
「トライアウト・チームは、常にスポッティングを重視してきましたが、今回は特にそれを心掛けました。成功の一因は、生産の初期段階で金型のテストを行い、トライアウト・プレスと同じ結果が得られると確認したことです。このように、デジタル・エンジニアリングでトライアウトの先まで見通すことによって、すべての不具合を正確に予測できるのです。大きな違いは、例えば、この金型工場で通常扱っているフードのアウターとインナーを加工する場合、インナー構造がアウターの形状を整えるためにアウターは見込み補正せず、インナー構造のみを見込み補正していました。しかし今までと比べ多くの構造部品を扱うことになり、エンジニアリングの段階であらゆる部品を見込み補正せざるを得なくなりました。私達の目標は±0.5mm以内で見込み補正することでした。」
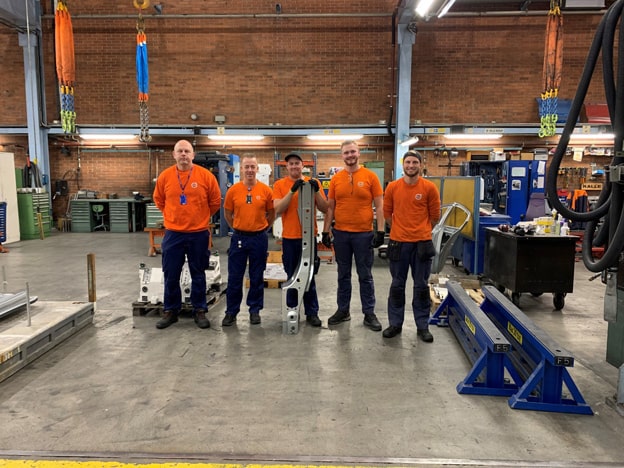
「また以前と異なる点として、今回はトリム型を含むドローシェルの見込み補正をデジタルで検討し、すべての金型にそれぞれ適した見込み補正を行いました。新しいワークフローの一環として、非常に複雑なシミュレーションを行い、徹底的に検討したのです。AHSSへの移行は、デジタル・エンジニアリングの比重が飛躍的に高まることを意味します。すべての金型の見込み補正を行い、それを適用することは、これまでにない新たな取り組みです。」
「確かに、AutoForm見込み補正ソリューションの精度について、当初は懐疑的であったことも事実です。しかし、先進的で成形が難しい部品でしたから、まずは試してみようと思いました。すべての作業を完了し、試作した部品を測定するまで、ソフトウェアの評価を下すことはできません。これまで経験したことのないものに直面すると、不安が生じるのは当然です。切削段階の開始時に、トライアウト・チームは難しい決断を迫られました。そのときこそ、デジタルな見込み補正が正確であることを信じ、信頼に基づく賭けに出る瞬間でした。このトライアウト、そしてプロジェクトが完了する頃には、この新たなソリューションが成功に導いてくれることを確信していました。ですから、成形が難しい材料であるにもかかわらず、予定日を大幅に前倒しする形で金型を完成できました。最期に1回の品質確認のためのトライアウトループを行っただけで、金型をプレス工場に納入できたのです。」

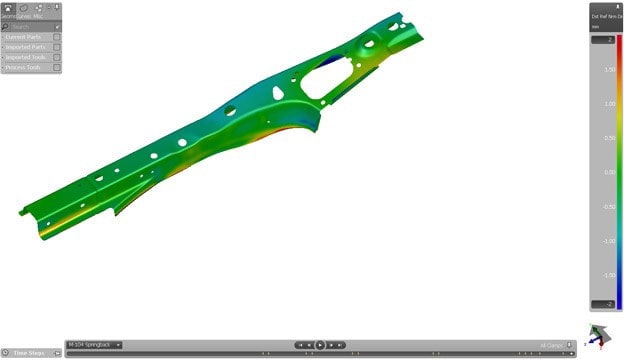
「私は一般の見込み補正機能の有用性を確信しました。これはAutoFormの非常にシンプルな機能ですが、品質確認ループでは非常に役立ちました。 今回の成功要因の1つは、スキャンしたデータのインポートが可能で、基準データと最初のトライアウト結果のベクトル・フィールドが作成できることでした。このベクトル・フィールドを2回目の見込み補正の検討に活用することで、短時間で目標に近付けることができます。これが、たった1回のループで成功した理由です。最初のトライアウトの結果は、AutoForm-Compensatorに基づくもので、品質確認ループは一般の見込み補正ツールのおかげで成功したのです。」
「組織にとっての価値は、エンジニアリングの努力がトライアウトで無駄にならないことです。チームにとっては、AHSSを使用したパネルの見込み補正はこれまでにない体験であり、通常より時間がかかりました。このように、現場に適用できる結果を得られたことは、今後、他の材料やパネルを扱う上で大きなメリットになることは明らかです。」
オロフストロムにあるボルボ社シミュレーション・チームの9名の皆さんに、祝辞を贈りたいと思います。